Il caso Sada Packaging
Nel nostro precedente articolo, abbiamo esplorato il potenziale trasformativo della metodologia 5S per ottimizzare l’efficienza e ridurre gli sprechi nei luoghi di lavoro.
Oggi, invece, vogliamo portarvi all’interno di un caso studio reale dove abbiamo avuto l’opportunità di applicare questi principi.
Questa esperienza non solo ha rafforzato la nostra competenza nella metodologia 5S, ma ha anche messo in luce come un approccio sistematico possa generare miglioramenti tangibili, incidendo positivamente sulle dinamiche operative e sulla qualità del lavoro.
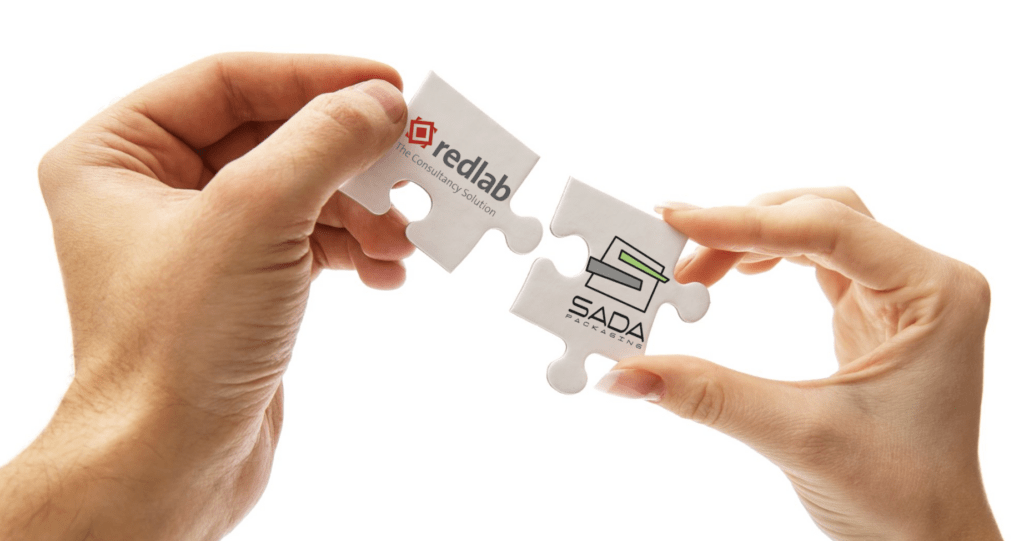
Il lavoro è stato svolto in collaborazione con Sada Packaging: la cartotecnica del Gruppo Sada nata nel 2006 che produce astucci in cartoncino teso e microonda con tecnologia offset.
Un’azienda giovane in grado di offrire un prodotto di alta qualità grazie alle tecnologie di ultimissima generazione con clienti nazionali e multinazionali dalle richieste molto esigenti, in particolare serve i settori Food e Consumer.
L’inizio del progetto di miglioramento è stato preceduto da un periodo di approfondita analisi, nel quale è emersa la necessità per Sada di ottimizzare il processo di Ondulazione. La percentuale iniziale di scarti ha costituito il motore propulsore per avviare un progetto di miglioramento incentrato sulla metodologia delle 5S.
Questo approccio si è concentrato sulla creazione di un ambiente di lavoro caratterizzato da: pulizia, ordine ed efficienza, promuovendo una cultura aziendale orientata al miglioramento continuo e all’ottimizzazione delle risorse.
Vediamo nel dettaglio di cosa ci siamo occupati
Seiri (Sort): il primo passo è stato quello di collaborare con i team sul campo per identificare e rimuovere gli oggetti non necessari dallo stabilimento. Gli elementi non necessari e poco utilizzati sono stati individuati e distinti con cartellini rossi, etichettando gli oggetti in base alla loro utilità o frequenza di utilizzo.
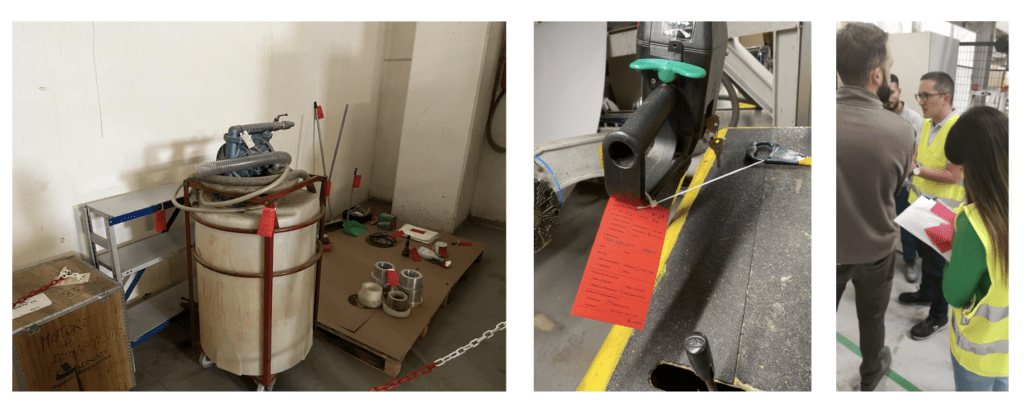
….
Seiton (Set in Order): successivamente, abbiamo allocato una posizione specifica per ogni attrezzatura e materiale necessario, assicurando un facile accesso e riducendo il tempo dedicato alla ricerca degli strumenti indispensabili.
….
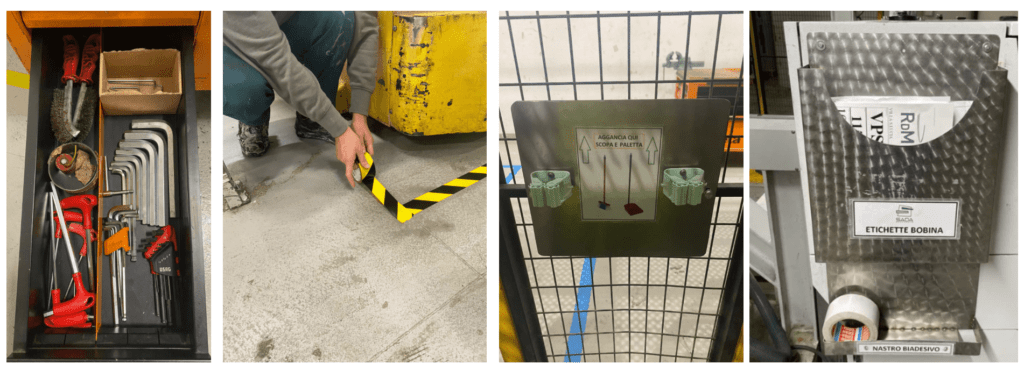
….
Seiso (Shine): in questa fase abbiamo attivamente collaborato con il personale aziendale, per stabilire routine di pulizia e manutenzione che andassero oltre la semplice pulizia superficiale.
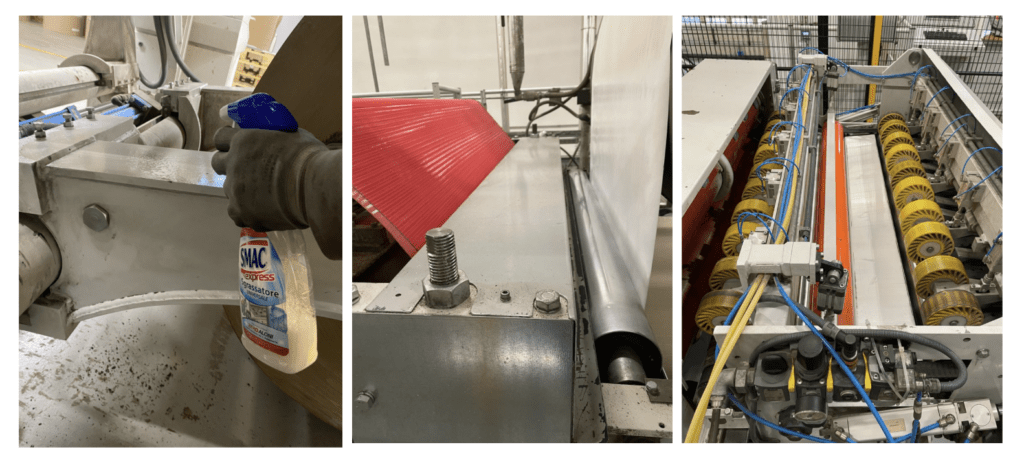
….
Seiketsu (Standardize): durante lo sviluppo della 4S sono state create regole e procedure chiare per mantenere le condizioni migliorate ottenute attraverso le prime 3 “S”. Ciò contribuisce a stabilizzare il processo e a garantire che gli standard di ordine, organizzazione e pulizia siano mantenuti nel tempo.
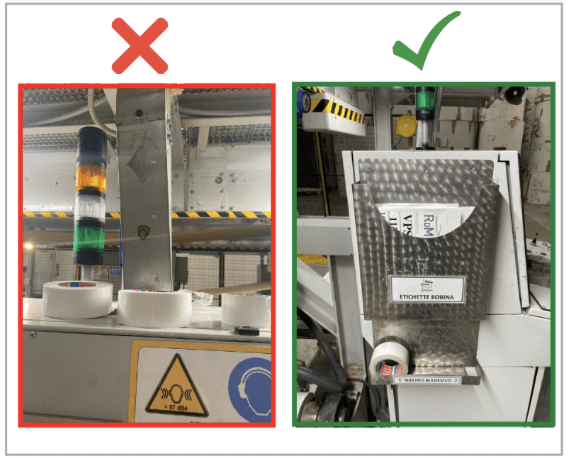
…
Shitsuke (Sustain): l’ultimo pilastro delle 5S riguarda il mantenimento delle regole, delle procedure e dei principi stabiliti durante l’implementazione delle prime quattro fasi. Nel dettaglio sono stati implementati degli audit periodici per garantire il rispetto degli standard e la risoluzione tempestiva di eventuali deviazioni.
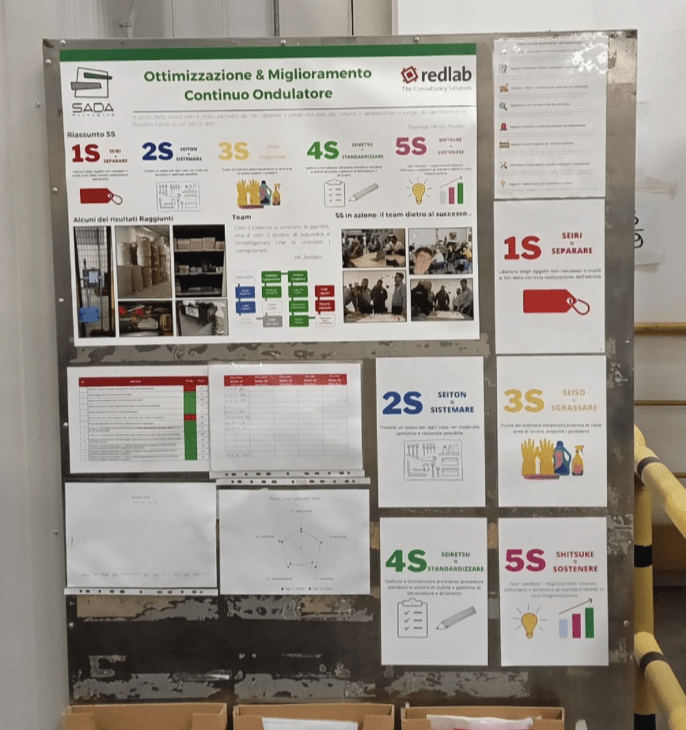
…
Grazie all’implementazione dei progetti si sono verificati miglioramenti significativi nelle aree di produzione interessate evidenziati da:
- Un ambiente di lavoro più ordinato, pulito e sicuro;
- Una riduzione della variabilità dei processi con aumento dell’efficienza e della produttività;
- Un impatto positivo sulle competenze, la motivazione e la cultura del personale, che ha contribuito a creare un ambiente di lavoro più efficace e orientato al miglioramento continuo.
….
Le storie di successo e i feedback positivi dei dipendenti evidenziano come la metodologia 5S abbia non solo migliorato l’ambiente fisico ma anche motivato il personale, promuovendo un senso di orgoglio e appartenenza.
….
Siamo fieri e molto felici del processo di implementazione e dei risultati ottenuti e ci auguriamo che questo sia solo il primo traguardo di grandi successi insieme!